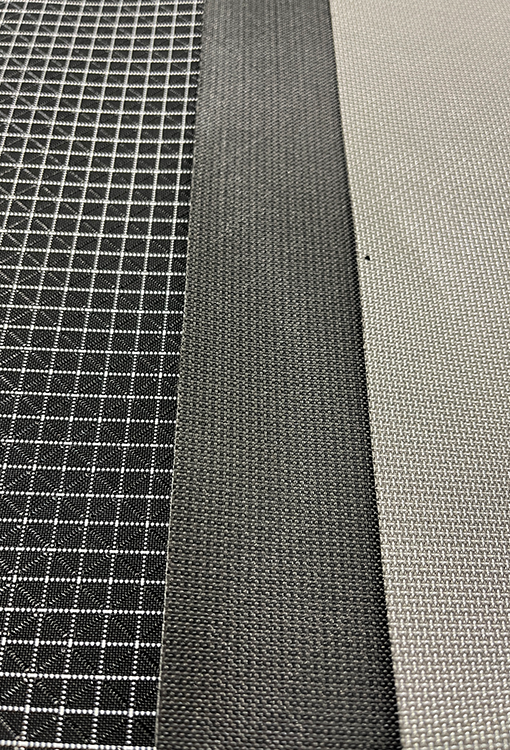
What’s the Difference Between Ultra and Robic Fabrics?
When choosing a backpack, the materials matter. Durability, weight, and water resistance can make or break your experience on the trail. At ULA Equipment, we use high-quality materials that stand up to the demands of serious hikers. Two of the most popular materials in the ultralight and durable backpacking world are Ultra fabrics and Ripstop Robic Nylon—but which one is right for you?
While Robic has been an incredibly durable and trustworthy material that we’ve utilized for over 2 decades, the new appeal and offering of lighter, stronger, and more waterproof laminated materials like Ultra has many reconsidering their priorities for ultralight adventure. We’ve had plenty of hikers put 10,000+ miles on their robic backpacks. Both of our Robic and Ultra fabrics are PFAS free so you only have to worry about leaving footprints behind. It’s important to note that in this article when we mention Ultra materials we’re specifically talking about UltraWeave as opposed to UltraGrid. We’ll cover UltraGrid in a separate article. We offer most all of our packs like the Circuit SV and Catalyst in both Ultra and Robic fabric options so keep this in mind as you read through.
Before we dive into the materials it’s important to mention the denier of the materials and how we talk about them. But what is denier?
DENIER
Denier (D) is a unit of measurement used to describe the thickness and weight of fibers in a fabric. It specifically refers to the mass in grams of 9,000 meters of a single fiber strand. The higher the denier number, the thicker and heavier the fibers are.
Low-denier fabrics, such as 15D and 30D, are lightweight and more flexible, offering a softer feel. However, they are less durable and more prone to tears. These materials are commonly used in ultralight gear, including sleeping bag shells and ultralight tents, where weight savings are prioritized over durability
High-denier fabrics, such as 210D, 420D, and 1000D+, are heavier and more rigid, offering superior abrasion resistance and durability. These materials are commonly used in rugged backpacks, heavy-duty outdoor gear, and luggage, where strength and longevity are prioritized over weight savings.
At ULA, we use 420-denier Ripstop Robic Nylon for its durability and reliability. Our Ultra fabric options range from 200D to 400D, balancing weight savings with strength.
When you see “Ultra 400 X” this is referring to a 400 denier Ultra(UHMWPE) material. This is a thicker material than “Ultra 200 X” The X in these refers to the laminated backing material and the “X” pattern it forms. So for example, we use 200 denier Ultra X on the less abrasion prone areas of the pack like the main body and collar, and 400 denier Ultra X on the parts of the pack that see more impact like the side pockets, bottom panel, and back panel.
What is Ultra Fabric?
Ultra fabrics are a new generation of ultralight and ultra-durable backpack materials. If you’re familiar with Dyneema or DCF materials, these are the most closely compared to Ultra. Ultra is constructed with a woven Ultra High Molecular Weight Polyethylene (UHMWPE) face fabric laminated to a waterproof film backing. This combination creates an incredibly strong, highly tear-resistant, and waterproof material. It’s important to note here that although Ultra as a material itself is waterproof, we do not seam seal our packs so you will still need to use a pack liner with your Ultra pack.
How is Ultra Fabric Made?
Ultra fabrics are engineered through a multi-step process to maximize strength, durability, and water resistance. The production process involves:
- Woven UHMPE/Polyester face: Ultra High Molecular Weight Polyethylene (UHMWPE) fibers are extruded and woven into a grid-like structure. These fibers are known for their exceptional strength-to-weight ratio, being 15 times stronger than steel per unit weight.
- Lamination Process: On the X and TX versions, an ULTRA “cross ply” is laminated below the face fabric. This provides dimensional stability as well as strength/tear benefits.
- Waterproof Film Application: A proprietary “RUV film” is laminated to the back of the fabric. This eliminates the need for traditional DWR (Durable Water Repellent) coatings and makes the material inherently waterproof.
- Heat and Pressure Bonding: The layers are fused together under high heat and pressure to create a single, durable, and lightweight material with zero stretch or deformation.
- Final Quality Control & Testing: The fabric undergoes rigorous strength, abrasion, and waterproofing tests to ensure it meets ultralight backpacking standards.
This advanced construction method results in a fabric that is extremely lightweight, abrasion-resistant, waterproof, and UV-resistant, making it one of the most high-performance materials available in backpacking gear.
PROS + CONS OF ULTRA
Key Benefits of Ultra Fabric:
- Superior Strength-to-Weight Ratio – Ultra fabric is twice as strong as comparable nylon fabrics while remaining extremely lightweight.
- Waterproof – The laminated construction eliminates the need for a DWR coating, making it naturally waterproof.
- Abrasion Resistant – The woven UHMWPE face fabric is more durable against wear and tear compared to traditional nylons.
- UV Resistance – Holds up better under prolonged sun exposure.
Potential Drawbacks:
- Price – Ultra fabrics are more expensive due to their advanced technology and construction.
- Stiffness – Some users find Ultra fabrics to be a bit more rigid compared to nylon-based materials. For travel bags like the Dragonfly, this rigidity is preferred.
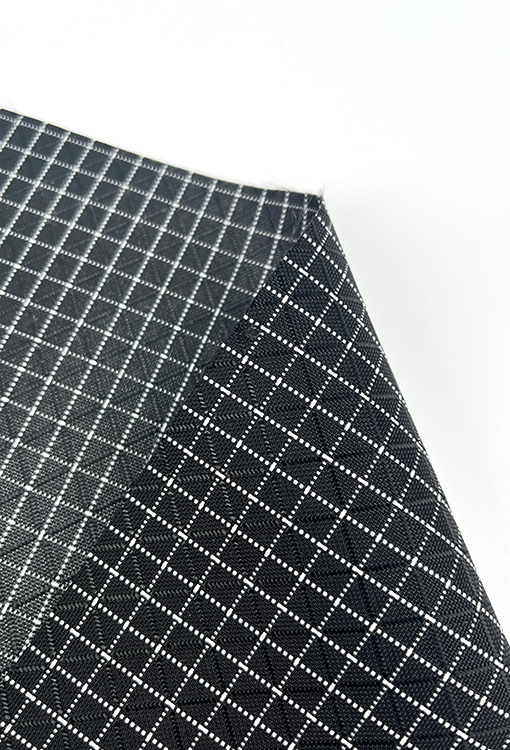
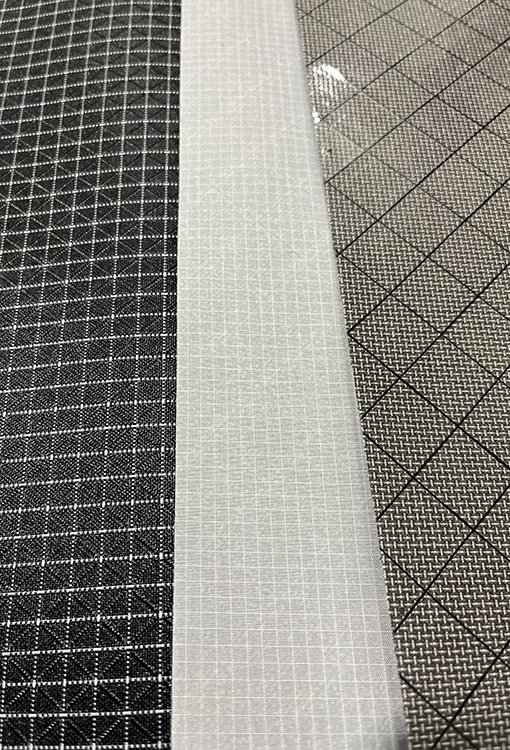
What is Ripstop Robic Nylon?
Ripstop Robic Nylon is a high-tenacity nylon fabric reinforced with a ripstop weave. This material has long been a go-to for durable backpack construction because of its excellent balance of strength, flexibility, and cost-effectiveness.
How is Ripstop Robic Nylon Made?
Ripstop Robic Nylon is a specialized high-tenacity nylon fabric designed for superior strength and durability. The manufacturing process includes the following steps:
- Polymer Preparation: Nylon 6 or Nylon 6,6 polymer granules are melted and extruded to form continuous filaments. These filaments are highly durable and have superior tensile strength.
- Yarn Formation: The extruded filaments are spun into high-tenacity yarns. The strength of these yarns contributes to the fabric’s ability to resist wear and tear. A 600D polyester is used for this.
- Ripstop Weaving Process: The fabric is woven using a special ripstop weave, which incorporates thicker, reinforced threads at regular intervals (typically every 5 to 8 mm). This creates a grid-like pattern that prevents small tears from spreading, enhancing durability. This creates the “grid” pattern in ripstop materials.
- Heat and Pressure Treatment: The woven fabric is subjected to a heat-setting process to stabilize its structure and improve dimensional stability.
- Coating and Finishing: To enhance water resistance, the fabric is treated with a Durable Water Repellent (DWR) coating. This DWR coating utilizes C0 pfas free DWRs.
- Quality Control Testing: The final fabric undergoes rigorous testing for tear strength, abrasion resistance, and coating durability to ensure it meets industry standards for outdoor gear.
This meticulous process results in a tough, reliable, and highly abrasion-resistant fabric that is both lightweight and flexible—making it an excellent choice for backpacking gear.
PROS + CONS OF ROBIC
Key Benefits of Ripstop Robic Nylon:
- Tough and Resilient – Robic nylon is one of the strongest forms of nylon available and resists tears well.
- More Affordable – Compared to Ultra fabrics, Robic nylon offers a solid balance of performance and cost.
- Proven Performance – This fabric has been trusted in backpacking for years, offering reliable durability and performance.
- More Easily Repaired – If you’ve got some panels that need a little love, replacing and repairing robic materials is significantly more streamlined than Ultra.
Potential Drawbacks:
- Heavier than Ultra fabrics – While still lightweight, Robic nylon doesn’t match the weight savings of Ultra fabrics.
- Requires a DWR Coating – Not naturally waterproof; relies on coatings to resist moisture.
- Less UV Resistant – Over time, extended sun exposure can weaken nylon fabrics more than Ultra fabrics.
Although Robic is technically not as durable as Ultra materials, we’ve still had thousands of hikers get 10,000 miles out of their Robic backpack.
Which One is Right for You?
Choosing between Ultra fabrics and Ripstop Robic Nylon comes down to your priorities as a backpacker:
- Go with Ultra fabrics if you want the lightest, strongest, and most waterproof option available and are willing to invest in premium materials.
- Go with Ripstop Robic Nylon if you want a cost-effective, reliable, and flexible material that still offers excellent durability.
At ULA Equipment, we offer both materials to give you the best options for your backpacking adventures. Whether you need a bombproof, waterproof pack made with Ultra fabrics or a durable, affordable Robic nylon backpack, we’ve got you covered.
The Bottom Line
Both Ultra fabrics and Ripstop Robic Nylon have their strengths. If weight savings and durability are your top concerns, Ultra fabrics are hard to beat. If you want a proven, flexible material at a lower cost, Ripstop Robic Nylon is an excellent choice.
No matter which material you choose, you can trust that ULA’s backpacks are built to handle the toughest trails out there. Which material do you prefer? Let us know in the comments!
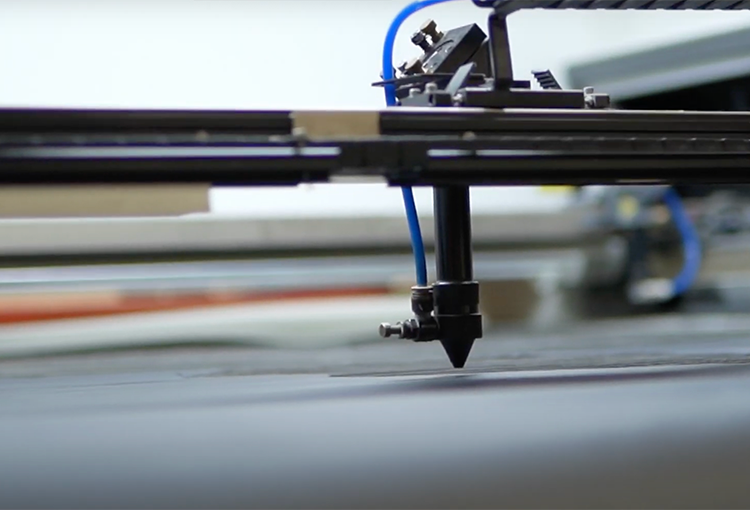
ULTRA IS SUCH A STRONG MATERIAL WE HAD TO BUY A LASER TO CUT IT.
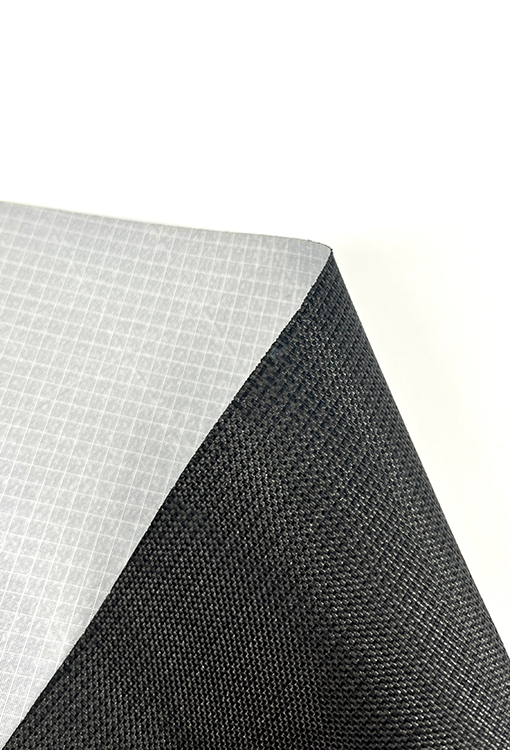
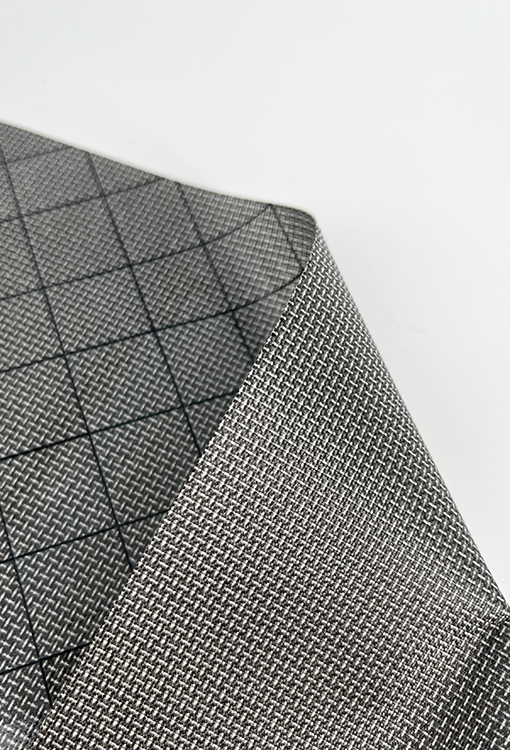
what is the weight difference for a Catalyst Pack between the two fabrics? I am getting ready to replace my old Catalyst.
Hey Joe,
You’d save a little over 4 ounces. Ultra saves about 10% of the weight total. Robic is 44.4 oz, ultra is 40.1 oz. Thanks! – Garrett
Great article. Curious why you don’t tape the ultra packs? Also is this something that a user can do at home?
Hey Victor, great question. We’ve seam taped in the past and it’s prone to become delaminated so instead of offloading the cost to you guys, we omit it. Another aspect of it is the repairability factor, since we offer in-house repairs, if a panel needs to be switched out the seam tape can hinder the process. – Garrett